NEW RT-Toolbox3 Robot Software: No Teach Pendant Required
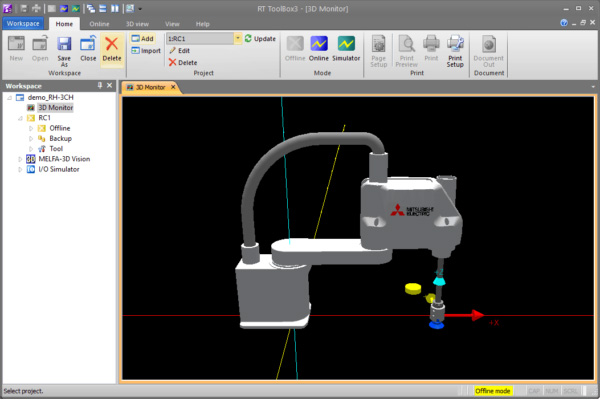
The newly released RT-Toolbox3 robot software is intuitive and easy to use. This full featured software allows a user to program, simulate, monitor and forecast maintenance for the robot. The very simple MELFA-Basic programming environment turns commissioning into child's play.
Simulation Functions:
Simulation that includes features such as robot dynamics and servo responses as well as robot controller emulation allows realistic simulations that include motor loading, tracking and positioning times.
- Programs that have been created can be executed in the PC, movements can be verified, and the tact times of specified parts of a program can be measured.
Such simulation functions are also effective for preliminary system examinations. - Servo simulations can also be performed, for preliminary examination of loads.
- Signals can be coordinated with GX works2 and GX works3 for easy creation of line simulators. A maximum of 8 robots can be operated, and coordinated movements among robots can be verified.
Monitoring Functions:
- As well as monitoring program run states, variables, input/output signals and other events, these functions can show graphs of robot operation waveforms (speeds and current values) and I/O states in real time.
- This makes it easy to see the correlation between program execution steps and waveform data, making debugging markedly more efficient.
Oscillograph Functions:
The oscillograph can display the graphical representation of a robot's various internal data.
The data acquired from the robot can be saved at a CSV file.
- Up to 80000 records of data including current position, speed, axial loading, and sensor information can be obtained in every operating cycle of the robot and displayed in a graph.
- Execution rows and I/O signals are recorded and used for analyzing the robot status, and this improves the debug efficiency.
- The obtained data can be saved as an image (Bitmap) or in the CSV format.
Maintenance Functions:
- With maintenance, you can maintain the robot in various ways, including setting origin data and initializing various informations.
- These functions include maintenance forecast, position recovery support, parameter management, etc.
- With "Maintenance forecasting", you can reference the parts replacement timing (greasing and battery and belt replacement) from operation data collected up till now in the robot controller.
- In addition to there are functions such as Position repair Function, Servo Monitor.
Security Function:
- It is possible to forbid access to the robot programs, parameters, and files in the robot controller.
- The security function can be achieved by setting a password in the robot controller. The robot controller software versions where this can be used are as follows.